
PRIMARY AND RECHARGEABLE BATTERIES
PRIMARY AND RECHARGEABLE BATTERIES
AETC celebrates its multi-year experience with battery electrochemistry. We make and test a variety of batteries and cells representing at least 15 commercially-viable cell chemistries. Most of our products are customized and are designed to fit form-factored applications which are often proprietary to our customers.
AETC celebrates its multi-year experience with battery electrochemistry. We make and test a variety of batteries and cells representing at least 15 commercially-viable cell chemistries. Most of our products are customized and are designed to fit form-factored applications which are often proprietary to our customers.
AETC celebrates its multi-year experience with battery electrochemistry. We make and test a variety of batteries and cells representing at least 15 commercially-viable cell chemistries. Most of our products are customized and are designed to fit form-factored applications which are often proprietary to our customers.
AETC celebrates its multi-year experience with battery electrochemistry. We make and test a variety of batteries and cells representing at least 15 commercially-viable cell chemistries. Most of our products are customized and are designed to fit form-factored applications which are often proprietary to our customers.
AETC introduces its capabilities in battery design and assembly. We take pride in our in-house production of a range of battery types, including alkaline, lithium primary, zinc air, and lithium ion batteries and their respective chemistries.
AETC introduces its capabilities in battery design and assembly. We take pride in our in-house production of a range of battery types, including alkaline, lithium primary, zinc air, and lithium ion batteries and their respective chemistries.
OTHER TECHNOLOGIES
AETC is also prominently experienced in several other technologies. This includes including nanomaterials, graphite electrodes and shapes, and metallurgical work. Reach out to AETC representatives if these products are of interest.
Nanomaterials
AETC is pleased to introduce its partnership with a world leader in nano-oxide ceramic materials manufacturing. Our products, which we offer mainly to the electrochemical industry, include bismuth oxide, nickel oxide, and aluminum oxide, and range in size anywhere from 40-400 nanometers.
At these ultra-fine particle sizes, the electrochemical and catalytic activity of the systems incorporating these oxides are greatly increased, as opposed to the activity demonstrated by micronized materials. Applications for nanomaterials range from new-gen catalysts for processing hydrogen gas in fuel cells, to creating a puncture-free layer of alumina on top of anode films for lithium-ion batteries, to hydrogen evolution suppressants in alkaline primary battery zinc anodes. Interested parties are encouraged to reach out to AETC to discuss what we can do for you.
Synthesis of Graphite Electrodes and Shapes
AETC boasts a capability of preparing customized extruded shapes of synthetic graphite with the addition of natural graphite and other materials. The electrodes employed by the industry range in size anywhere from 8′-42′ in diameter and can take huge shapes and heavy weights. AETC makes test electrodes with a nominal diameter of 1”, and these are used for pre-feasibility studies.
At these ultra-fine particle sizes, the electrochemical and catalytic activity of the systems incorporating these oxides are greatly increased, as opposed to the activity demonstrated by micronized materials. Applications for nanomaterials range from new-gen catalysts for processing hydrogen gas in fuel cells, to creating a puncture-free layer of alumina on top of anode films for lithium-ion batteries, to hydrogen evolution suppressants in alkaline primary battery zinc anodes. Interested parties are encouraged to reach out to AETC to discuss what we can do for you.

Molten Iron Billets Solidifying

Manufacture of Shapes

Nanoceramics

Electrodes in AETC's Laboratory
Compositional graphite electrodes are synthesized using carefully-calculated proprietary recipes. The bulk of the electrode is made out of calcined needle coke which, upon graphitization, turns into synthetic graphite. However, there are several other components, such as: pitch binder, natural graphite, iron oxide, boron oxide, and/or several other additives which are mixed into the electrode composition for various reasons. Ultra-high-power (UHP) electrodes use pin stock to connect two long pieces of electrode together, and demand several pitch impregnations and other exclusive requirements to maximize strength and conductivity. Interestingly, in order to make the electrode more conductive, some natural graphite or other additives are needed, which in turn cause the deterioration of the overall density of the material. The idea is for these electrodes to create a very strong shape with both electrical conductivity and mechanical strength being as high as possible, so a great deal of optimization is required in order to balance out the multiple factors that affect these traits.
Another subset of the extruded graphite electrode market is that of smaller-sized, electrically conductive graphite rods, bars, and sheet stock. These shapes are used in the making and development of pore-free electrically conductive formulations, and understandably have a different set of requirements from UHP electrodes when it comes to starting particle size of granules. For instance, smaller-diameter rods could use synthetic graphite of <10 microns particle size, drastically differing from the case of EAF electrodes, where graphite can be as large as ¾”. Furthermore, these small-particle, pore-free formulations also require a unique optimization process for their various components, even though the process of baking, graphitization, and pitch impregnation may seem similar to that of UHP electrodes.
In production plants, the recipe is set on a daily basis. In our labs, AETC is able to extrude, bake, impregnate, re-bake, and machine electrode shapes of 1” diameter. Even though the electrode is small, it allows us to analyze and predict how easily components may be mixed together. We can discern how fine the materials should be or how they should be processed together, for example, and we can determine the general suitability of certain materials for application as additives in the electrode industry. Those interested, especially parties who provide all types of synthetic graphite, natural graphite, or boron additives, are encouraged to contact AETC and discuss how we qualify into the electrode industry.
Metallurgical
AETC is involved in a variety of metallurgical testwork, made possible by industry connections and our access to high-tech advanced equipment and technologies.
We conduct experiments on creating grey iron and ductile iron out of steel scrap by melting scrap steel together with carbon. For that purpose, we offer our customers access to our induction furnace, which can support batches of up to 200kg, and which heats and melts metal to create alloys with specific characteristics. Properties of the resultant alloy are determined using the most advanced ASTM-referenced mechanical tests in a certified testing laboratory.
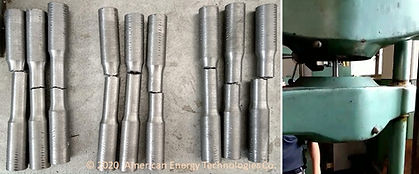
Tensile Strength on Steel Samples
AETC leverages its industry connections to qualify new and improved carbon materials for applications in steel mills as re-carburizers. Even when making highly-sophisticated battery-grade carbon materials, there is always going to be some material which is out of specification. Re-carburizers are an excellent market for taking such material and finding value-added uses for it. However, there are some alloys that present problems (which are especially relevant to manufacturers of automobile engine components in particular). These alloys have to do with ductile iron, which is very difficult to make. This application cannot use out-of-spec material from other industries: it has to be customized, premium-performance premium-grade carbon material of very high purity, extremely low in nitrogen and sulfur. We can produce a material that possesses the proper particle sizes, density, and meltability by molten metal. It requires tedious optimization work, but the rewards are high.
Another subset of metallurgical applications is one known as melt cover. Melt cover is based on de-sulfurized forms of synthetic graphite, or, alternatively, for certain types of steel-making, it is based on expandable graphite. Expandable graphite is a special form of processed natural flake which has excellent thermal conductivity and makes for a great high-temperature suppressant, so it can be used effectively in melt-cover applications for either maintaining a constant temperature or cooling off the temperature of the furnace melting pot.
AETC offers several lucrative in-house technologies for preparing synthetic or natural graphite for use in melt-cover and re-carburizer applications, doing detailed and precise metallurgical work and guaranteeing manufacturers success as they gain access into market niches which command premium profit margins, while at the same time providing very large sales volumes.

Melt Cover

Steelmaking at AETC